What is Porosity in Welding: Necessary Tips for Getting Flawless Welds
Wiki Article
The Science Behind Porosity: A Comprehensive Overview for Welders and Fabricators
Recognizing the complex devices behind porosity in welding is vital for welders and producers pursuing impeccable craftsmanship. As metalworkers look into the midsts of this phenomenon, they discover a globe governed by numerous variables that affect the development of these tiny voids within welds. From the make-up of the base materials to the ins and outs of the welding procedure itself, a wide range of variables conspire to either intensify or relieve the visibility of porosity. In this detailed overview, we will certainly decipher the scientific research behind porosity, discovering its impacts on weld top quality and introduction progressed methods for its control. Join us on this trip via the microcosm of welding flaws, where precision satisfies understanding in the pursuit of remarkable welds.Understanding Porosity in Welding
FIRST SENTENCE:
Exam of porosity in welding exposes critical insights right into the integrity and quality of the weld joint. Porosity, identified by the visibility of cavities or voids within the weld metal, is a typical concern in welding processes. These gaps, otherwise properly addressed, can jeopardize the architectural honesty and mechanical buildings of the weld, bring about possible failings in the ended up item.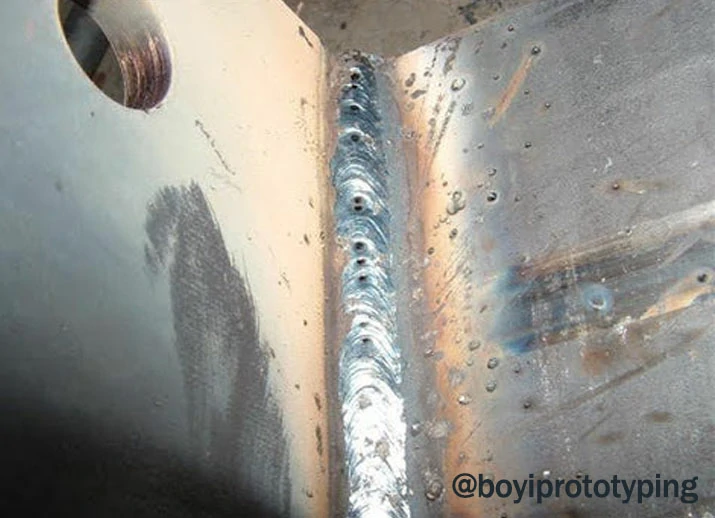
To discover and measure porosity, non-destructive screening techniques such as ultrasonic screening or X-ray assessment are commonly utilized. These methods enable the identification of internal problems without jeopardizing the stability of the weld. By examining the size, shape, and distribution of porosity within a weld, welders can make enlightened choices to enhance their welding procedures and achieve sounder weld joints.
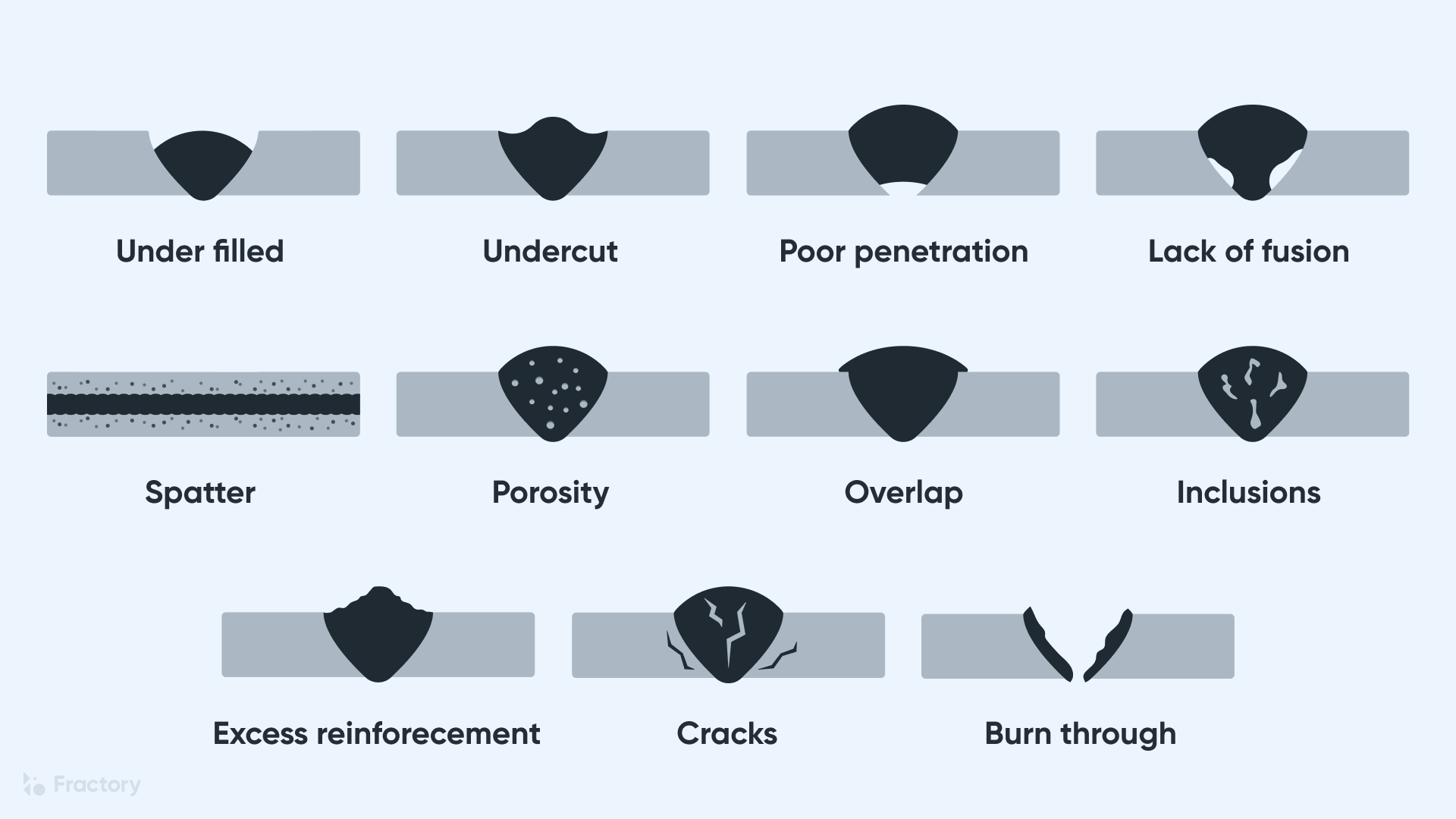
Elements Influencing Porosity Formation
The occurrence of porosity in welding is influenced by a myriad of factors, ranging from gas securing performance to the ins and outs of welding specification settings. One essential aspect contributing to porosity formation is poor gas securing. When the protecting gas, usually argon or CO2, is not effectively covering the weld swimming pool, atmospheric gases like oxygen and nitrogen can pollute the liquified metal, resulting in porosity. Furthermore, the tidiness of the base materials plays a significant duty. Pollutants such as rust, oil, or dampness can vaporize throughout welding, producing gas pockets within the weld. Welding parameters, including voltage, existing, take a trip speed, and electrode type, also impact porosity development. Making use of incorrect setups can generate too much spatter or heat input, which in turn can result in porosity. In addition, the welding technique used, such as gas steel arc welding (GMAW) or protected metal arc welding (SMAW), can affect porosity formation because of variants in warmth circulation and gas insurance coverage. Understanding and regulating these factors basics are important for decreasing porosity in welding procedures.Results of Porosity on Weld Top Quality
Porosity formation considerably jeopardizes the structural stability and mechanical homes of bonded joints. When porosity is existing in a weld, it develops gaps or cavities within the material, reducing the overall strength of the joint. These spaces function as anxiety focus factors, making the weld extra at risk to cracking and failure under load. The presence of porosity also compromises the weld's resistance to corrosion, as the trapped air or gases within the spaces can react with the surrounding atmosphere, causing deterioration gradually. Additionally, porosity can hinder the weld's ability to stand up to stress or effect, additional jeopardizing the overall top quality and integrity of the bonded structure. In crucial applications such as check this aerospace, automotive, or structural buildings, where safety and security and resilience are vital, the harmful effects of porosity on weld high quality can have extreme consequences, emphasizing the importance of minimizing porosity via appropriate welding methods and procedures.Methods to Minimize Porosity
In addition, making use of the appropriate welding specifications, such as the right voltage, existing, and travel speed, is important in protecting against porosity. Maintaining a consistent arc length and angle during welding additionally aids decrease the possibility of porosity.
Making use of the proper welding method, such as back-stepping or employing a weaving activity, can additionally help disperse warm equally and minimize the chances of porosity development. By executing these techniques, welders can successfully minimize porosity and generate top quality welded Click Here joints.

Advanced Solutions for Porosity Control
Carrying out advanced modern technologies and ingenious methods plays an essential role in attaining exceptional control over porosity in welding procedures. One sophisticated solution is the usage of advanced gas blends. Shielding gases like helium or a blend of argon and hydrogen can help in reducing porosity by providing much better arc security and improved gas insurance coverage. Additionally, using advanced welding methods such as pulsed MIG welding or changed environment welding can additionally help minimize porosity issues.One more sophisticated remedy involves using innovative welding tools. As an example, utilizing devices with integrated functions like waveform control and sophisticated source of power can enhance weld high quality and minimize porosity risks. The application of automated welding systems with precise control over parameters can considerably reduce porosity issues.
Moreover, incorporating advanced surveillance and evaluation modern technologies such as real-time X-ray imaging or automated ultrasonic screening can aid in detecting porosity early in the welding process, enabling prompt restorative actions. In general, integrating these innovative remedies can substantially boost porosity control and improve the overall quality of bonded elements.
Conclusion
In conclusion, comprehending the scientific research behind porosity in welding is essential for welders and producers to produce top notch welds - What is Porosity. Advanced services for porosity control can better enhance the welding procedure and ensure a solid and reliable weld.Report this wiki page